Innovations in Sustainability in Chemical Production
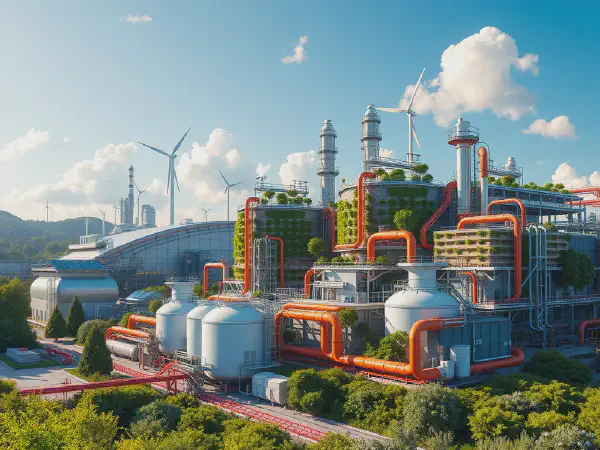
Sustainability in Chemical Production
Sustainability in Chemical Production is a vital aspect of today’s industrial landscape, focusing on minimizing environmental impact while maintaining efficient production processes. This approach emphasizes responsible resource usage, waste management, and the reduction of carbon footprints in chemical manufacturing. As the global demand for chemicals continues to grow, the sustainability agenda becomes increasingly essential to ensure that production methods do not compromise the earth's ecological balance.
The transition towards Sustainability in Chemical Production marks a significant shift in how industries operate. Implementing green practices in chemical production not only enhances operational efficiency but also aligns companies with the growing demand for environmentally friendly products. The focus is on innovative strategies that integrate sustainability into every phase of production, from raw material sourcing to end-of-life disposal of chemical products.
Moreover, the concept of Sustainability in Chemical Production extends to the use of renewable resources, energy efficiency, and the adoption of safer chemical processes. By engaging in sustainable practices, companies can reduce energy consumption, lower waste generation, and minimize hazardous emissions. This not only benefits the environment but also improves the overall economic performance of chemical companies by reducing costs associated with energy and waste management.
As stakeholders increasingly prioritize corporate sustainability, chemical producers are responding by developing comprehensive sustainability frameworks that include social, economic, and environmental dimensions. This holistic approach ensures that Sustainability in Chemical Production is not merely a trend but a fundamental and lasting transformation in the industry.
Ultimately, the journey towards Sustainability in Chemical Production requires collaboration between government, industry, and academia to innovate and implement solutions that facilitate sustainable chemical processes. By embracing this change, the chemical sector can take a leadership role in promoting environmental stewardship while meeting global chemical demands.
Green Chemistry Practices
The principles of Green Chemistry serve as a guideline for developing sustainable chemical processes. These principles promote the use of safer chemical substances, the elimination of toxic by-products, and the reduction of energy consumption throughout the chemical lifecycle. By adhering to these principles, chemical manufacturers can significantly lessen their environmental impact and enhance the safety and sustainability of their products.
In practical applications, Green Chemistry can be observed in various industrial settings—ranging from pharmaceutical production to the synthesis of agrochemicals. For instance, the use of alternative solvents, such as water or biodegradable materials, instead of harmful organic solvents, demonstrates how Green Chemistry practices can be integrated into conventional chemical processes, improving both safety and sustainability.
Furthermore, numerous case studies across the industry highlight successful green initiatives, such as the development of bio-based feedstocks for polymer production. Companies implementing these practices not only enhance their sustainability credentials but often achieve cost savings and efficiency gains through reduced raw material and energy use.
Biodegradable Materials
Biodegradable materials, including bioplastics and organic composites, are at the forefront of innovation in sustainable chemical production. These materials can decompose naturally under specific conditions, minimizing environmental pollution compared to traditional plastics. Types of biodegradable materials are rapidly evolving, incorporating renewable resources such as corn starch, potato starch, or polylactic acid (PLA) in their formulation.
The impact of biodegradable materials on chemical production is significant, as they allow manufacturers to reduce reliance on fossil fuels and lessen environmental footprints associated with commonly used plastics. This shift promotes a circular economy, where materials are continually cycled through the production process and waste generation is significantly reduced.
Future trends in biodegradable innovations are promising, with ongoing research focusing on enhancing the properties of these materials and their broad application in industries ranging from packaging to automotive. As consumer demand for sustainable products increases, the chemical industry must continue to adapt and invest in the development of biodegradable alternatives.
Energy Efficiency in Production Processes
Enhancing energy efficiency in chemical production is another critical element in pursuit of sustainability. Techniques such as process optimization, heat integration, and utilizing energy-efficient equipment are instrumental in reducing energy consumption. By applying these techniques, manufacturers can significantly lower their operational costs and environmental impact.
Innovative technologies, such as advanced manufacturing processes and automation, play a crucial role in reducing energy consumption. For instance, the adoption of continuous flow reactors has proven to be more energy-efficient compared to traditional batch processing. Such innovations not only streamline production but also decrease the carbon footprint of chemical manufacturing operations.
The impact of energy efficiency on sustainability is profound; by reducing energy consumption, chemical producers can contribute to lower greenhouse gas emissions and mitigate climate change effects. Additionally, energy-efficient processes enhance the resilience of companies against fluctuating energy prices, providing them with a competitive advantage in the market.
Waste Reduction Techniques
Implementing waste reduction techniques is essential for promoting sustainability in chemical production. Methods such as source reduction—where unnecessary materials are eliminated from production processes—and process modifications can significantly curb the generation of chemical waste. Companies are encouraged to adopt a mindset focused on minimizing waste throughout the production lifecycle.
Recycling processes in chemical production also play a significant role in waste reduction. Reclaiming solvents or recovering valuable materials from waste streams not only reduces landfill disposal but also conserves resources and saves on raw material costs. Effective recycling systems can lead to closed-loop processes, enhancing resource efficiency within manufacturing operations.
The overall impact of waste reduction on environmental sustainability is substantial. By minimizing waste generation and promoting recycling, chemical companies can decrease their environmental footprint and contribute positively toward a sustainable future. Moreover, this not only complies with regulatory standards but also resonates with environmentally-conscious consumers.
Regulatory Impacts on Sustainability
Regulations promoting sustainability in the chemical industry are diverse, encompassing various international standards and protocols aimed at reducing environmental impacts. These regulations often focus on controlling emissions, encouraging waste minimization, and promoting the use of green technologies. Adhering to such regulations is crucial for chemical manufacturers aiming to enhance their sustainability practices and reputation.
The impact of policies on chemical production is significant, as regulations can incentivize or mandate the adoption of sustainable practices. Companies that proactively comply with regulations often gain a competitive edge through enhanced public perception and increased customer loyalty, aligning their operations with societal expectations regarding environmental responsibility.
Numerous companies have successfully adapted to sustainability-focused regulations, showcasing innovative compliance strategies that demonstrate their commitment to sustainable development. These case studies highlight the potential benefits of regulatory alignment, including improved operational efficiency, reduced environmental impact, and enhanced market positioning in an increasingly eco-conscious economy.