Top Safety Standards in Chemical Manufacturing: 2023 Update
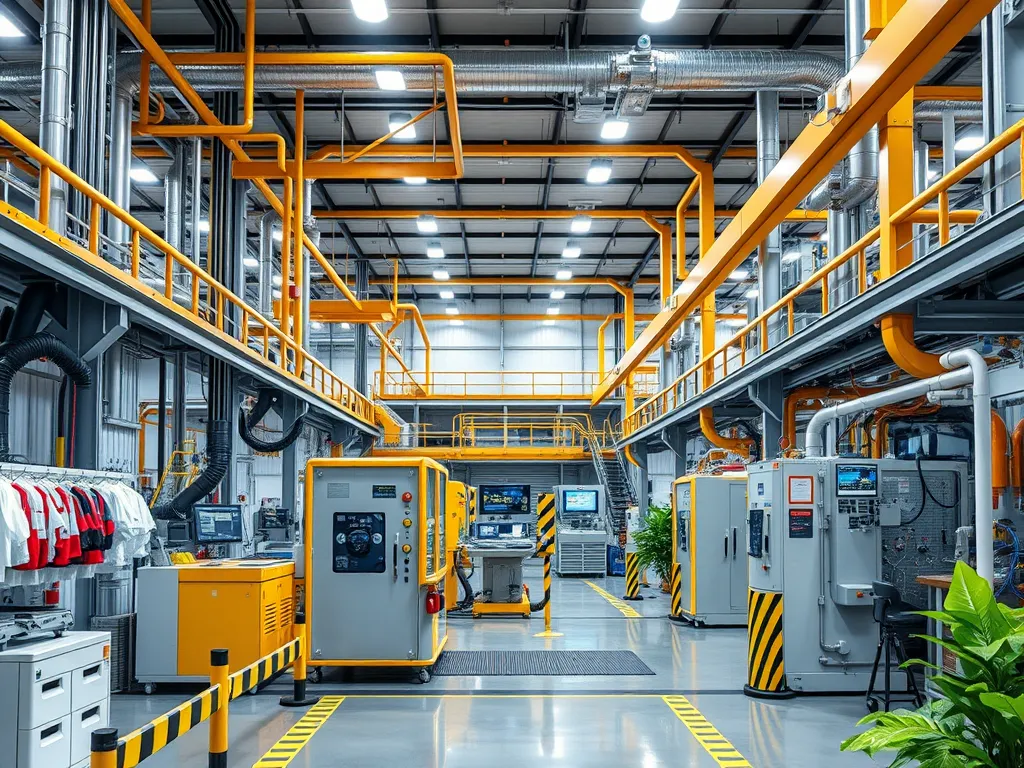
Safety Standards in Chemical Manufacturing
Safety standards in chemical manufacturing are essential to ensure the well-being of employees, the public, and the environment. Given the hazardous nature of many chemicals used in manufacturing processes, these standards provide guidelines for safe handling, storage, and disposal. Adhering to safety standards minimizes risks and promotes a culture of safety within the organization, contributing to overall operational efficiency and regulatory compliance.
The importance of safety standards in chemical manufacturing cannot be overstated. They help to identify potential hazards before they become incidents, facilitate training and awareness among employees, and ensure the safe operation of equipment and processes. In this highly regulated industry, compliance with safety standards is not just a recommendation; it is a legal requirement that helps companies avoid severe penalties and reputational damage.
Implementing safety standards fosters an environment of continuous improvement where safety practices are regularly evaluated and updated. This dynamic approach ensures that organizations can adapt to changing regulations, technology advancements, and emerging safety challenges. Companies that prioritize safety standards are often recognized for their commitment to health and safety, which can lead to improved employee morale and retention, as well as enhanced public trust.
Safety Standards in Chemical Manufacturing encompass a wide range of regulations and best practices, including risk assessment, proper use of personal protective equipment (PPE), emergency response planning, and employee training. These components work together to create a comprehensive safety management system that addresses the unique challenges posed by hazardous materials and processes in chemical manufacturing.
Ultimately, the goal of safety standards in chemical manufacturing is to protect lives, property, and the environment. By investing in safety compliance and fostering a safety-conscious culture, companies can mitigate risks, enhance operational performance, and contribute to the sustainable development of the industry.
Regulatory Compliance
Understanding OSHA regulations for chemical manufacturers is crucial for maintaining a safe workplace. The Occupational Safety and Health Administration (OSHA) sets forth guidelines that chemical manufacturers must adhere to, including proper labeling of hazardous chemicals, employee training, and maintaining Material Safety Data Sheets (MSDS). These regulations ensure that employees are informed about the risks associated with chemical exposure and that appropriate safety measures are in place to protect them.
EPA standards and their impact on safety are another important aspect of regulatory compliance in chemical manufacturing. The Environmental Protection Agency (EPA) regulates the release of hazardous substances into the environment, requiring manufacturers to comply with emission standards and reporting requirements. This not only protects the environment but also encourages companies to implement more sustainable practices that can reduce their overall risk exposure.
International safety standards comparison highlights the varying requirements across different regions and sectors. Organizations that operate globally must navigate the complexities of compliance with multiple regulatory frameworks, such as the Globally Harmonized System (GHS) for classification and labeling of chemicals. Understanding these differences is vital for multinational companies to maintain safety standards and meet the expectations of various stakeholders.
Hazardous Materials Management
Best practices for handling hazardous chemicals are critical to ensuring safety in chemical manufacturing. This includes proper storage techniques, regular inspections, and minimizing the use of hazardous substances whenever possible. Organizations should develop comprehensive hazardous materials management plans that outline procedures for safe handling, transportation, and disposal of chemicals, reducing the likelihood of accidents and spills.
Risk assessment techniques in chemical manufacturing involve identifying potential hazards, analyzing the likelihood of their occurrence, and implementing strategies to mitigate them. By conducting thorough risk assessments, companies can prioritize safety interventions and allocate resources effectively to address the most significant risks in their operations.
Training employees on hazardous material safety is essential to maintaining a safe work environment. Regular training sessions should cover topics such as proper handling techniques, emergency response procedures, and the use of personal protective equipment (PPE). An informed workforce is critical in preventing accidents and ensuring compliance with safety standards.
Safety Equipment and Technology
Essential safety equipment for chemical plants includes personal protective equipment (PPE), spill containment kits, ventilation systems, and emergency safety showers. Investing in high-quality safety equipment not only protects employees but also reduces the risk of costly accidents and regulatory fines.
The role of technology in enhancing safety standards is increasingly significant in chemical manufacturing. Advanced technologies such as real-time monitoring systems, automated controls, and data analytics enable manufacturers to detect potential hazards early and respond proactively to minimize risks. Implementing these technologies can lead to safer work environments and improved overall safety performance.
Innovative safety solutions in chemical manufacturing include the use of drones for inspections, wearable safety technology for real-time health monitoring, and predictive maintenance tools. These innovations not only enhance safety protocols but also contribute to greater operational efficiency and cost savings.
Emergency Preparedness and Response
Developing effective emergency response plans is essential for chemical manufacturers to address potential incidents promptly. These plans should outline clear procedures for responding to various emergencies, such as chemical spills, fires, or explosions, ensuring that employees know their roles and responsibilities in such situations.
Safety drills and training for chemical spills are crucial to reinforce emergency preparedness. Regular practice of emergency scenarios allows employees to become familiar with response procedures, reducing panic and improving efficiency during real emergencies.
Coordination with local emergency services is vital for a comprehensive emergency response strategy. Establishing relationships with local fire departments, medical services, and hazardous materials teams ensures that chemical manufacturers can respond effectively to emergencies, minimizing harm to employees and the surrounding community.
Continuous Improvement in Safety Practices
Implementing a culture of safety in chemical manufacturing involves promoting safety as a core value within the organization. This requires leadership commitment, employee involvement, and open communication about safety concerns. Organizations that foster a culture of safety are more likely to see positive outcomes in employee engagement and incident reduction.
Regular safety audits and inspections help organizations identify areas for improvement and ensure compliance with safety standards. By systematically reviewing safety practices, manufacturers can implement necessary changes and reinforce a proactive approach to safety management.
Feedback mechanisms for safety improvements, such as safety committees and anonymous reporting systems, empower employees to share their observations and concerns. Encouraging open dialogue about safety fosters a collaborative environment where continuous improvement is valued and prioritized.